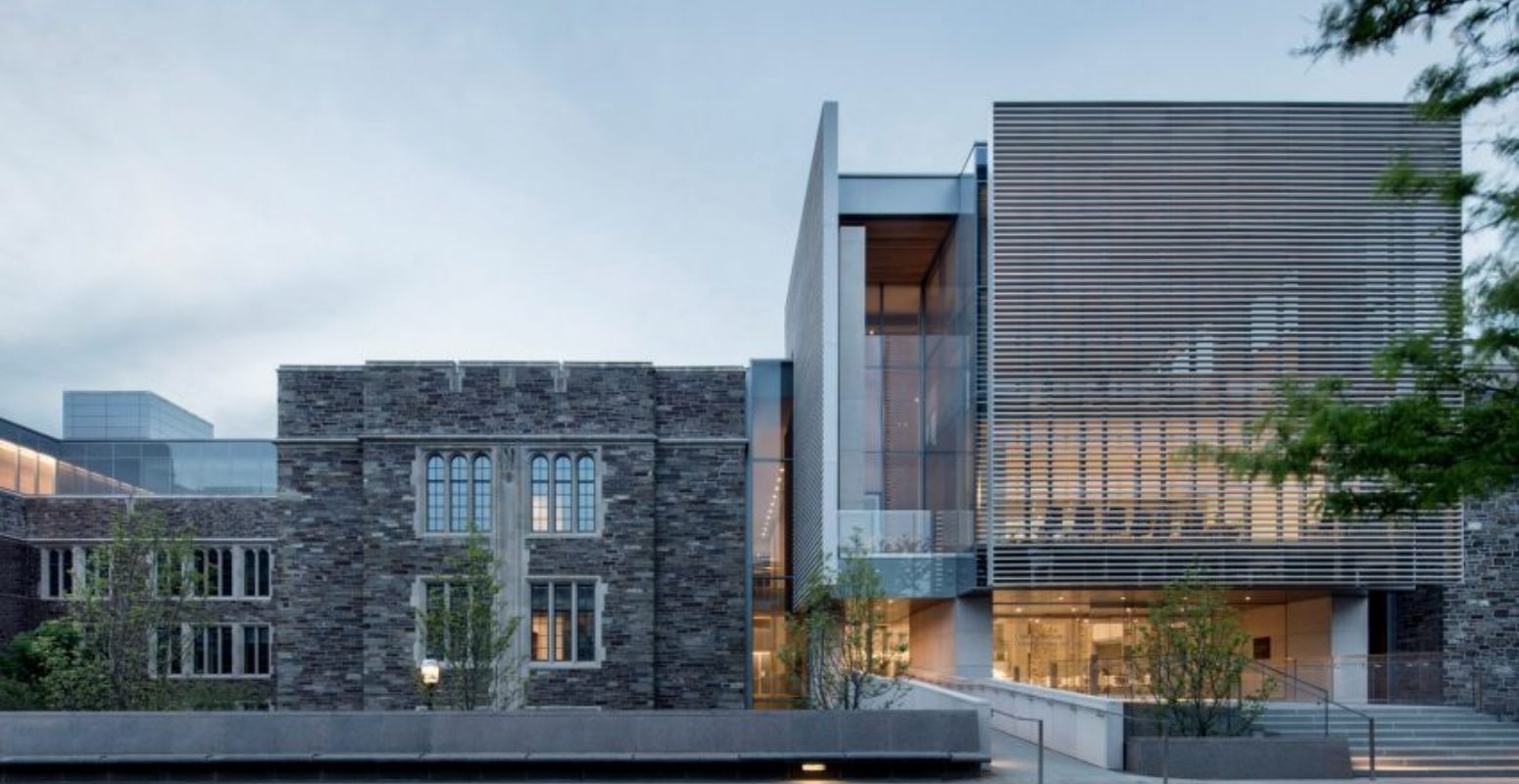
Leaving The Doubters Behind: Addressing the Preconceptions
Breaking down preconceptions of off-site housing has proved a difficult task in the past, but advancements in both the manufacturing and design processes are significant, and show no signs of abating. Wayne Yeomans, of B&K Structures, had this to say:
“I think that for my generation and older, say 40 upwards, there has always been a tendency to look down on prefabricated or modular buildings. A lot of us went to school in classrooms that were essentially portacabins which had been built off-site. These were hot in the summer, freezing in the winter and severely lacking in character. The changes that we have seen, even in the last ten years alone, are tremendous.”
The UK’s historical shift towards modular building came off the back of the second world war. The spare factory capacity and techniques for swift assembly which were first used for the war industry became a way to increase housing delivery fast, and at a time when it was most needed.
These units were only intended to have life-spans of around ten years, but stood for much longer than that. Take the Excalibur Estate in Catford, built in 1945/46. 187 prefabricated bungalows which should have been taken out of use long before they were finally demolished in 2013...
Oliver Booth of Gardiner and Theobald added:
“Even the vernacular itself is negative - ‘prefab’ has connotations of housing which is cheap, thrown-together and substandard. Whereas the same can’t be said for younger homebuyers and renters, who are more open to the idea of off-site constructed housing. This is for the simple reason that they haven’t grown up with awareness of any of the issues or stigma that their parents’ generation has previously attached to it.
“There is also something of a snobbery associated with assembly-line manufacturing as well”, picks up Wayne. “The car industry is an example of how strange that is, once you have thought about it. You wouldn’t think twice about buying an assembly-line car, which is about as precision engineered a piece of manufacturing as anything within the consumer market. This provides a parallel for the advancement of the off-site construction processes and materials as well - think about the disdain that Skoda cars used to be treated with, and compare that to their historic, off-site manufacturing equivalents in the construction industry. Now compare the advances over there, where they are now considered to be high-quality, Volkswagen-engineered vehicles, with the advancements around construction in general. You could argue that the advances in housing are considerably more impressive than the automobile equivalents.”
David Lomax, of Waugh Thistleton was also able to cast further light on the conversation.
"One of the points worth making is the strange disconnect that persists about quality. It’s not just unpleasant to be working in the wind and the rain, it’s also a factor for consistently producing good workmanship. We simply can’t expect to be achieving the same quality on a building site with wet, messy materials and difficult conditions as we would expect to achieve in the dry, safe, controlled conditions of a factory. However, the perception of low quality persists from the products we used in our prefab buildings post war, not just in the pre-fab low rise estates, but in the panellised concrete structures we continued to build well into the 60s.
I would say that this is where utilising increasing levels of off-site comes to the fore. It’s not just the process that needs to change, it’s the materials too. Previously pre-fab buildings have been made from lots of little components, screwed and glued together than loaded onto a lorry. Each time we fix two things together, we have an opportunity for error, poor quality or future splits and cracks which let water in and heat out.
With off-site, there is a mental shift. Instead of trying to build new machines for processes that were designed for human hands and scale, a precision off-site building works with much larger format panels than a human would previously have been able to manipulate, and is suited to the skills our machines already have - in cutting and shaping with incredible accuracy. By using large format materials and eliminating many fine grain processes we are able to increase the input of machines and reduce the potential for error, therefore making better quality buildings. We didn’t have the wrong machines before - we had the wrong materials.
This, of course, leads to a digital-led, 'indoor' future within the industry which is more attractive to a workforce which expects, in much greater numbers, to graduate from university and work within a highly-skilled sector. In our next post, we look at the skills shortage in the industry and how the rise of digital-based precision engineering can lead to a sea change in how the construction experts of the future can expect to deliver the housing that Britain needs.
Many thanks to our good friends Wayne Yeomans (B and K Structures), David Lomax (Waugh Thistleton) and Oliver Booth (Gardiner and Theobold) for their signifcant input into this article. All are doing great work in the sector, and since its writing have picked up a number of awards at this year's Structural Timber Awards.