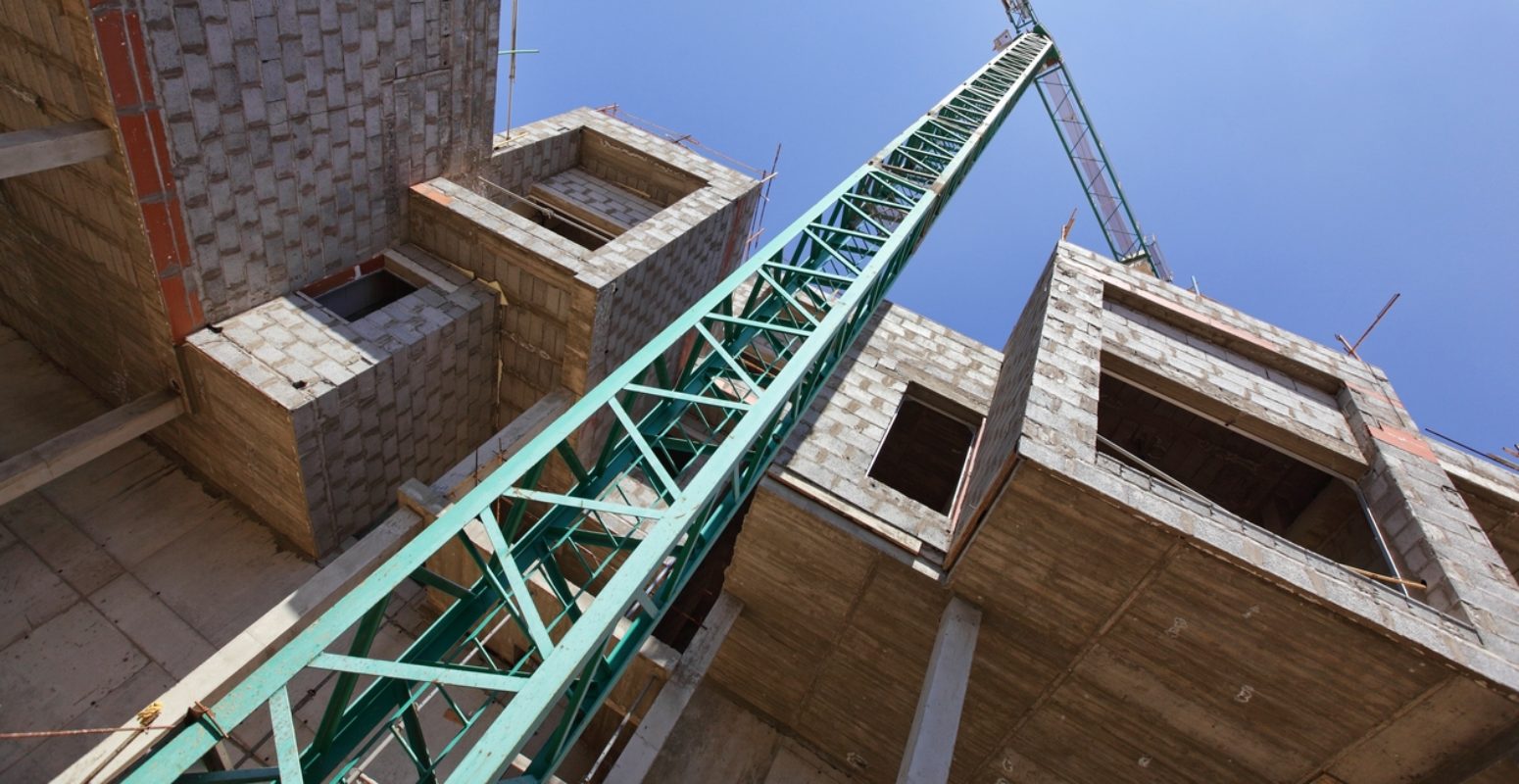
A New Generation: How Off-Site Construction Can Help To Attract Top Young Talent
As highlighted in Mark Farmer’s industry review of 2016 entitled Modernise or Die, the construction industry’s ageing workforce is contributing to a rising differential between the amount of homes built and that which is required to meet an increasing national shortfall. 'Signed, Sealed, Delivered', the recent GLA report on the potential solutions offered to London by offsite-manufacturing, touches on the industry’s pioneering technological advances as a way of engaging the talent of the next generation, ergo ensuring the industry's survival. As Nicky Gavron AM suggests in the report's recommendations, ‘being able to offer professional 'careers' in a permanent place of work should help the industry attract a broader pool of talent - especially women and young people.’
This is a point which Andrea Schrader of architectural practice Ackroyd Lowrie is quick to back up. "By introducing more progressive thinking and a design and technology focus, the construction industry can become a more appealing choice for younger generations, with much greater diversity in the workforce than we see today. Women make up a mere 11% of our industries today, of which only 4% are qualified professionals. A recent study by the CITB states that only 4% of the workforce is ethnic origin, compared with a higher average of 10% in the UK population as a whole. These statistics are much the same for wider STEM industries. There is room for improvement and I believe off-site construction can play a valuable part in that change".
Millienials don’t really recognise traditions such as “this is the way it has always been done”. They want to challenge the norms with smarter, more efficient, and - key to their generation - more sustainable ways to build.
Moving the industry indoors to a permanent location and displaying its longevity are both attractive attributes for the engineers and delivery experts of the future. Wayne Yeomans of B&K Structures makes the point that “traditional construction has a reputation as a luddite industry. If you were to transport a Roman bricklayer from a building site 2,000 years ago, and drop him onto one now, the chances are that he’d pretty much be able to do that job within a day or two. Isn’t that crazy? Surely this makes construction one of the slowest industries to progress, full stop - lay a brick, move on and lay another. However, the advent of off-site manufactured housing should lead to a sea change in approach. It's precision engineering, in a safe and secure location. It helps to move construction away from being an outdoor industry, in the cold, rain and wind. Young people have a chance to hone their skills and apply themselves in a much more modern, high-tech environment, and it is advances like this which make off-site solutions such a positive step for the future of the industry”.
Dave Lomax of Waugh Thistleton agrees. “This dovetails with Mark Farmer’s point about the desirability of construction as a profession. Since the late nineties era, the government's aspiration has been to get 50% of our school leavers into higher education. That means those who’ve landed on a construction site feel they’ve failed in comparison to their peers - even if you and I know they’re probably as well off if not more so! We aren’t going to change that perception by simply putting the same processes under a roof. Instead, we should mobilise our ambitious, tech-savvy workforce into learning new skills in working with machines and processes in an ambitious and forward-looking construction industry. Staff can be trained in specific skills for the delivery of homes and other buildings in factories, and take the same pride as they would do by training and working as an engineer in a Boeing, BAE or Rolls Royce factory”.
It is approaches such as this that encourage positivity about the changing face of off-site manufactured construction and its growing appeal to those entering employment after graduating from university.
Ian Hargreaves and Ellie Davies of Buro Happold also add their thoughts. “Our graduates and engineers are all highly-educated millennials who finish university with the ability to model and design buildings in 3D. Throughout their degrees they work collaboratively with other units within the total design project process, rather than having the narrow view that comes with a discipline-specific focus. As a result, they don’t really recognise traditions such as 'this is the way it has always been done'. They want to challenge the norms with smarter, more efficient, and - key to their generation - more sustainable ways to build. Offsite prefabrication delivers all of these requirements. Working together with other millennial designers and builders who have a similar holistic viewpoint, they can deliver buildings virtually which can be constructed quickly, cleanly and with zero clashes”.
Thanks to Morley Von Sternberg for the portrait photography used here. You can find more of Morley's work here:
Huge thanks also go to all of the individuals and organisations who contributed to this comment piece. To find out more about Hadley's work in this arena, please do tweet us at @hadleyproperty ,or write to us at info@hadleypg.com with questions and comments...